Společnost AGC spustila v severočeském Dubí Na začátku roku linku Volta běžící z poloviny na elektřinu. Country manažer skupiny AGC Miloslav Zoula v rozhovoru s Ekonews popisuje, jaké možnosti dekarbonizace se pro odvětví výroby skla otevírají.
Sklářský gigant AGC v Evropě sází na postupnou elektrifikaci tavení, zkoumá možnosti využití amoniaku a dalších paliv. „Celková koncepce dekarbonizace v České republice není jasně stanovená. Těžko se nám tak zaměřuje řešení pro naše závody,“ popisuje v rozhovoru pro Ekonews Miloslav Zoula.
„I z toho důvodu se nedržíme jedné varianty, ale máme připravených několik alternativ navázaných na konkrétní stav připravenosti české infrastruktury a kapacit zelených bezemisních zdrojů,“ doplňuje.
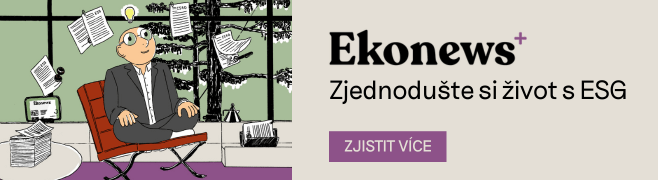
AGC Glass Europe sídlící v belgické Lovani je největším výrobcem plochého skla ve střední a východní Evropě. Firma patřící do japonské skupiny AGC v Česku vlastní pět výrobních závodů. Zaměřuje se na ploché sklo pro automobilový průmysl, stavebnictví a specializovaná průmyslová odvětví. Většinu produkce vyváží do zahraničí.
Máte stanovený cíl dekarbonizace do roku 2050. Jak ho máte rozplánovaný?
Hlavní náš cíl je dosáhnutí karbonové neutrality do roku 2050, který máme stanovený jednoznačně, a je to i cíl celé Evropské unie. Aktuálně připravujeme konkrétní strategii pro jednotlivé závody a máme ji rozdělenou na postupné kroky. Prvním konkrétním krokem je snížení našich emisí do roku 2030 o 30 procent pro Scope 1 a 2. Referenční je pro nás rok 2019. Tyto naše hlavní cíle máme certifikované externími organizacemi za celou společnost AGC v Evropě a aktuálně rozpracováváme detailnější strategii, jak toho dosáhnout u konkrétních závodů. V závodě Řetenice máme i specifický cíl v rámci naší automobilové divize. Pro výrobní linky vyrábějící autoskla plánujeme dosáhnout uhlíkové neutrality pro Scope 1 a 2 již do roku 2040.
Necháváte si měřit uhlíkovou stopu? Jaké máte výsledky a k čemu data využíváte?
Měříme a reportujeme uhlíkovou stopu všech našich evropských závodů. Stará se o to naše centrální oddělení. Data používáme k úpravě našich strategií pro jednotlivé milníky, kterými jsou roky 2030, 2040 a 2050. Samozřejmě je také sdílíme s našimi partnery a zákazníky. Mnoho z nich má nastavené vlastní cíle a potřebují od nás jako dodavatele konkrétní data. Naše automobilová divize je v tomto ohledu velmi aktivní a je to dáno cíli a požadavky našich zákazníků v automobilovém průmyslu.
Co tvoří největší část vaší uhlíkové stopy?
Uhlíková stopa výroby plochého skla se skládá z 48 procent z přímých emisí, vznikajících při samotném výrobním procesu, zejména při tavení a spotřebě surovin. Dalších 37 procent tvoří emise z dodavatelského řetězce. Nejmenší část, 15 procent, připadá na nepřímé emise spojené se spotřebou ostatních energií mimo vlastní tavení, především jde o spotřebu elektřiny, páry a technických plynů.
Co je pro sklářství největší překážkou při snižování uhlíkové stopy?
Výzev je mnoho. Za prvé jsou to technologické překážky, stávající technologie tavení se zásadně nezměnila mnoho desetiletí. Další výzvou v procesu dekarbonizace jsou jí vyvolané náklady, a tím pádem dlouhodobá ekonomická udržitelnost výroby. Sklářství je energeticky náročné, takže jsme na cenu energií velmi senzitivní ve výsledných cenách našich výrobků. Náklady na „zelenou“ energii pro tavení v porovnání se zemním plynem s výhledem do roku 2030 jsou více než čtyřnásobné.
Další velký problém se týká konkrétně České republiky. Celková národní koncepce dekarbonizace není definovaná. Těžko se nám tak zaměřuje naše vlastní cesta pro závody a dodržují stanovené termíny. I z toho důvodu se nedržíme jedné varianty, ale máme připraveno několik alternativ navázaných na konkrétní stav připravenosti české infrastruktury a kapacit bezemisních zdrojů i cen zelených energií. Naše plány jsou postavené konkrétně do roku 2030 a dále, abychom mohli reagovat na reálný vývoj. Budeme i velmi závislí na schválení národního plánu dekarbonizace průmyslu a stanoveného časového plánu.
Které inovace považujete za nejperspektivnější pro snižování uhlíkové stopy ve sklářském průmyslu?
Sledujeme všechny možnosti. Jejich vývoji se věnují naše výzkumné ústavy jak v Belgii, tak v Japonsku. V Evropě se kvůli místním podmínkám zaměřujeme na výrazné zvýšení podílu elektrického tavení při výrobě plochého skla. První z poloviny elektrifikovanou linku s příznačným názvem Volta jsme spustili letos v závodě Barevka. Dalšími nyní pro nás dostupnými zelenými palivy, která bychom mohli využívat, jsou především bioplyn, vodík a amoniak. Věnujeme se i těmto experimentálním technologiím. V Japonsku je například již v provozu jedna linka s částečným využitím amoniaku.
Jaké alternativní zdroje energie plánujete v praxi použít?
Nejlépe pro nás vychází využití elektrické energie, jde o námi preferovanou technologii. Z mého pohledu je to nejschůdnější cesta v Evropě. Mapujeme ale i budoucí možnosti nákupu bioplynu, zeleného nebo modrého vodíku a amoniaku. Máme přehled o konkrétních zdrojích a jejich výkonech, které mohou být v České republice do roku 2035. Vzhledem k tomu, že národní strategie jejich rozvoje neexistuje, tak kontaktujeme firmy či asociace v okolí České republiky, které jsou aktivní v řešení dekarbonizace. Je to ale náročné. Stejně jako my hledají cesty, mapují potenciály a možnosti do budoucna.
Zvažujete vodíkový pohon?
Vodík aktuálně experimentálně nevyužíváme, ale dostupné technologie již existují. Podobně jako u amoniaku je velký problém z hlediska infrastruktury. Je složité je dostat přímo do závodu. Zelený vodík je v dnešní době nejdražší palivo, které se dá k dekarbonizaci sklářství využít.
Budujete vlastní zelené zdroje?
Aktuálně dbáme na maximální využití odpadního tepla. Co se týče přímo zdrojů, jsme výrobci skla, takže v této oblasti spolupracujeme spíše s partnery, kteří budou pro nás výrobu zajišťovat. V západní Evropě máme již větrné elektrárny, na které jsou napojené naše výroby. Spíše ale mapujeme finanční náročnost a kapacitu zelené energie, kterou budeme schopni do budoucna nakoupit.
Bude potřeba u sklářství zachytávání vyprodukovaného oxidu uhličitého?
Vychází nám, že v dnešní době pro dosažení uhlíkové neutrality ve výrobě plochého skla nestačí nasadit lepší procesy tavení a využít jen zelené energie. Téměř určitě bude potřeba přistoupit k jímání, ukládání nebo druhotnému využití oxidu uhličitého z našich spalin. Zaměřujeme se tedy i na tyto technologie. Česká republika má z hlediska koncepce infrastruktury transportu CO2 oproti západní Evropě opět zpoždění. Kapacity, které bychom potřebovali, v tuzemsku nejsou a vysoce pravděpodobně nebudou před rokem 2035.
Využíváte při výrobě skla recyklovanou složku?
Snažíme se ji postupně navyšovat. Sklo je totiž nekonečně recyklovatelné a je velká škoda, pokud se opět nedostane do primární výroby. V tomto ohledu mají výhodu výrobci obalového skla, protože oni nejsou tak zaměření na výslednou kvalitu a barevnou čistotu.
U výroby plochého skla pro automobilový průmysl máme recyklaci zvládnutou velmi dobře. V Řetenicích již dnes využíváme zhruba 50 procent recyklované složky a pracujeme na vyšší míře recyklace díky vráceným autosklům ve spolupráci se třetími stranami. Trochu jiná je situace u plochého stavebního skla, protože recyklace skla z budov je velmi náročná. Aktuálně jsme u stavebního plochého skla schopni používat zhruba čtvrtinový podíl recyklovaného skla.
Pilotním projektem je v tomto opět linka Volta, která počítá až s 80procentním využitím recyklovaného skla. A samozřejmě máme strategii zvýšení podílu recyklovaného skla pro všechny evropské závody. Již dnes využíváme vysoký podíl střepů pro výrobu nízkouhlíkového stavebního skla.
Zabýváte se také uhlíkovou stopou vstupních surovin?
Jak jsem již nastínil, měříme celou naši uhlíkovou stopu za Scope 1, 2 i 3. Počítáme veškeré emise vzniklé v našem dodavatelském řetězci. U výroby a těžby surovin na základě dat upravujeme naši nákupní strategii. Můžu uvést i konkrétní příklad, kdy dovážíme přírodní sodu až z Turecka. V Evropě, především v Polsku, se vyrábí syntetická soda, ale ta má vyšší uhlíkovou stopu než přírodní. Porovnáváme celkovou emisní stopu a snažíme se vždy dosáhnout v konečném výrobku co nejnižší hodnoty.
Jak suroviny dopravujete?
U našeho největšího závodu na výrobu plochého skla v Řetenicích dovážíme suroviny ze tří čtvrtin vlakem, potažmo lodí a následně vlakem přímo do našeho závodu. Tento způsob přepravy surovin preferujeme nejen z hlediska emisí. Vnímáme i to, jak je vytížená kapacita silniční dopravy v celé Evropě.
Využíváte dotační programy nebo jiné formy podpory pro dekarbonizační opatření? Jaké jsou vaše zkušenosti?
Investice do dekarbonizace jsou velmi vysoké, ačkoliv se zatím pohybujeme na úrovni experimentálních technologií v malém nebo středním měřítku. Snažíme se proto různé dotační programy využívat. Zdůraznil bych, že máme problém čerpat dotace na národní úrovni, protože programy pro výrobce, kteří jsou zařazeni do procesu emisních povolenek, jsou nastavené relativně striktně a jsou pro nás těžko dosažitelné. Máme projekty, u kterých na národní úrovni nejsme schopni dosáhnout podpory, ale na úrovni Evropské komise ano. Příkladem byla i linka Volta.
Miloslav Zoula
Působí jako Country manažer skupiny AGC v České republice. Zároveň vede od roku 2019 závod AGC Flat Glass Czech v Teplicích-Řetenicích, kde se vyrábí ploché sklo jak stavební, tak pro automobily. Ve společnosti působí od roku 1998, kdy do ní nastoupil jako investiční specialista pro řízení výstavby. Podílel se na výstavbě a rekonstrukci klíčových sklářských závodů v tuzemsku i zahraničí.